- India is rapidly adopting electric vehicles (EVs) with annual sales exceeding 1.2 million in 2022-2023. However, this surge raises concerns about the life and demand of EV batteries.
- India currently relies heavily on imports for lithium-ion EV batteries. However, there is a growing push to support domestic EV industry development, thereby fostering economic growth and job opportunities.
- Materials from old EV batteries can be extracted through the recycling process, but battery recycling is highly capital-intensive and there is no existing market guide pricing and supply-demand dynamics. India must therefore, address these gaps to start recycling EV batteries at a large scale.
The adoption of electric vehicles (EVs) is witnessing a swift expansion around the globe, driven by the growing emphasis of governments and demand from consumers for low-emission transportation options.
India, a rapidly emerging market for EVs, currently has over 2.3 million EV users. In the financial year 2022-23, India’s annual EV sales surpassed 1.2 million, marking a 174% increase from the previous year. More than 60% of these sales were electric two-wheelers, while passenger electric three-wheelers accounted for 29% of the total units sold, as reported in the Annual India EV Report Card published earlier this year by consulting firm, JMK Research. More than half of the three-wheelers registered in India in 2022 were electric, according to an International Energy Agency (IEA) report published in April.
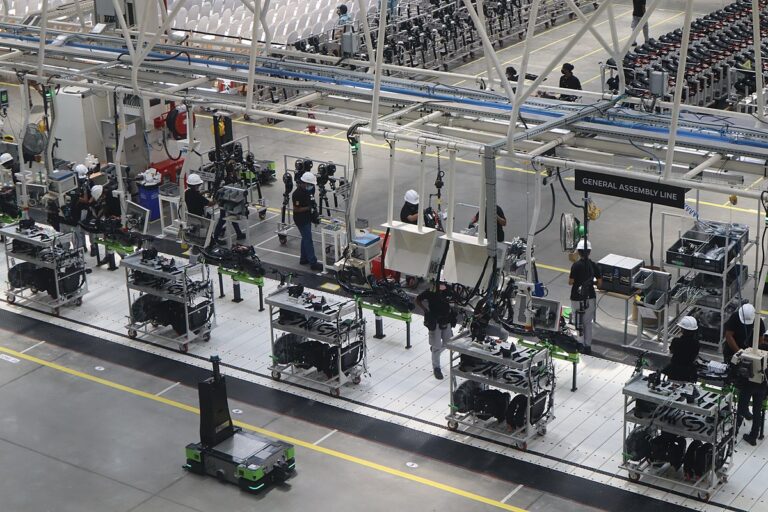
As the use of EVs grows around the world, there is also a growing need for EV batteries. This demand has led to significant growth in battery production. By 2030, it’s expected that there will be over five terawatt hours (TWh) of gigafactory capacity globally each year. ‘Gigafactory’ is a term popularised by the automobile company Tesla, which essentially means a large-scale EV battery manufacturing facility. For context, the country Senegal consumed about five terawatt hours (5,300 gigawatt hours per year) of electricity in 2021. India’s electricity consumption was around 1400 terawatt hours (1,442,000 gigawatt hours per year) as of 2021.
EVs are powered by lithium-ion (Li-ion) batteries. Therefore, with the increasing demand for EVs, the demand for Li-ion batteries is also set to increase. In 2021, the global lithium market was valued at $6.83 billion and it is projected to grow at an annual rate of 12 percent from 2022 to 2030. As of 2021, the global lithium production amounted to 100,000 tonnes (equivalent to 90.7 million kilograms), while the worldwide reserves are estimated to be around 22 million tonnes (equivalent to 20 billion kg), according to data from the U.S. Geological Survey.
Priti Mahesh, the Chief Program Coordinator of the non-profit Toxics Link, told Mongabay-India, “With such rapid growth expected in the global lithium market, it’s important to understand the necessary materials for the production of EV batteries, its battery recycling market and how this will impact the future of EV batteries.”
What are the components of a Li-ion battery?
Electric vehicle batteries come in different configurations, encompassing various shapes and sizes. Manufacturers have a multitude of choices when it comes to battery design, spanning from the physical structure of the cells to their chemical composition.
Batteries can be categorised into two main groups – primary batteries (also known as single-use batteries), which cannot be recharged and secondary batteries, which are rechargeable. Lithium-ion batteries belong to the latter category, as they can be charged and reused multiple times.
Explaining the composition and structure of lithium-ion batteries, Mahesh states, “In addition to lithium, a lithium-ion battery contains various other components and the manufacturing process involves multiple layers. Like most batteries, lithium-ion batteries consist of a positively charged cathode, a negatively charged anode, and an electrolyte that separates them. Typically, the cathode is composed of a mixture of lithium, nickel, cobalt, and manganese, while graphite is the most common choice for the anode. To protect and hold the individual cells together, lithium-ion batteries are enclosed in either an aluminium or steel casing, safeguarding them against mechanical damage.”
EV batteries typically consist of hundreds of cells, allowing each battery pack to maintain its charging and discharging capabilities for a range of 100,000 to 200,000 miles (1,60,934 to 3,21,868 kilometres), shares Mahesh. This confidence in battery durability is reflected in manufacturers’ common practice of offering extended warranties, often covering eight years or 100,000 miles for their electric vehicles (EVs).
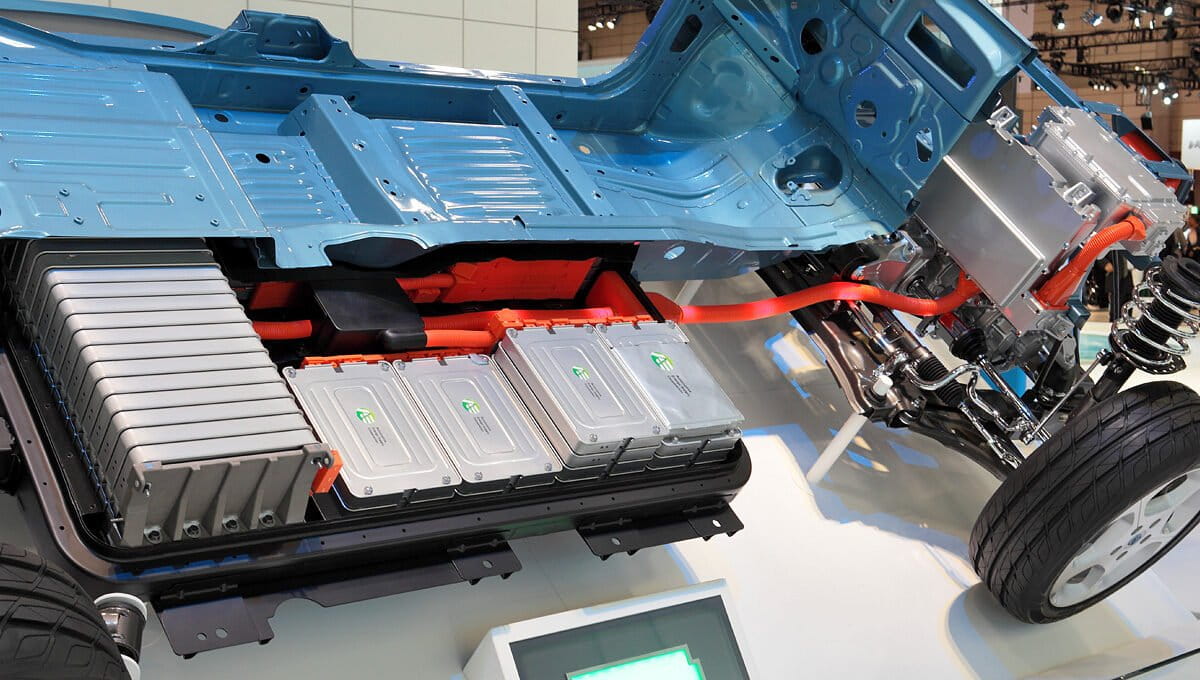
Typically, automobile Original Equipment Manufacturers (OEMs) such as Ola Electric and Ather Energy provide a standard three-year warranty for the batteries in their EVs. However, these batteries can potentially exceed this warranty period and last up to five years or more, contingent on factors such as usage patterns, environmental conditions and the effectiveness of the battery charging process.
Batteries used in two and three-wheelers are generally designed to withstand approximately 2,000 cycles of charging and discharging. In cases where EVs are employed for commercial purposes, the battery may wear out in as little as two years. Private vehicle batteries tend to have a longer lifespan, but for those engaging in extended journeys, battery replacement may become necessary within three years.
Moreover, current EV batteries have a lifespan of approximately 15 to 20 years within the vehicle, and they may even have a second life after this initial period. This extended longevity is complemented by ongoing advancements in EV battery technology, which are expected to result in batteries that last even longer, while also becoming more cost-effective, smaller in size and easier to transport.
Can India become self-reliant in EV battery manufacturing?
India’s ambition to expand its EV programme and bolster domestic manufacturing faces a significant challenge in ensuring a stable supply of raw materials for battery cells. At present, India heavily relies on imports, primarily from China, for Li-ion batteries and cells due to limited local cell manufacturing.
Rishabh Jain, Senior Programme Lead at The Council on Energy, Environment and Water (CEEW), elaborates, “This dependence on imports makes India’s EV industry vulnerable to global supply chain uncertainties and risks. However, there is a growing push to reduce import reliance and promote self-reliance to keep more of the value chain within India, thereby fostering economic growth and job opportunities. Policy initiatives like the Faster Adoption and Manufacturing of (Hybrid &) Electric Vehicles (FAME II) scheme and the Production-Linked Incentives (PLI) scheme are designed to support domestic industry development. FAME II encourages EV equipment manufacturers to source at least 50% of their components locally, while the PLI scheme targets Advanced Chemistry Cell (ACC) manufacturers.”
To address material security, India is also focusing on expanding mining exploration both within the country and overseas. India has joined the Minerals Security Partnership (MSP), a global alliance led by the United States, to catalyse investment in critical mineral supply and value chains. These strategies aim to increase domestic battery availability, reduce imports and lower battery costs while ensuring access to key raw materials like lithium, nickel, cobalt, and manganese, which constitute a significant portion of cell costs.
A CEEW study, titled How can India Indigenise Lithium-Ion Battery Manufacturing? authored by Rishabh Jain, highlights the critical importance of India gaining more control over the supply chain of lithium-ion batteries. Jain emphasises that considering the complexity of the global supply chain, it becomes imperative to develop an energy storage ecosystem, scale up battery cell manufacturing, and stabilise it to align with India’s decarbonisation objectives. “Additionally, the focus should be squarely on battery recycling as a means to reduce the demand for new minerals,” he adds.
Read more: In the EV era, Bengaluru startups innovate for a more sustainable battery ecosystem
Can EV batteries be recycled to mine minerals?
When we are producing so many batteries already, can the minerals locked inside the batteries be extracted to produce new batteries? Anumita Roy Chowdhury, Executive Director at the Centre for Science and Environment (CSE), believes this is possible. Studies on a global scale have shown that the material trapped inside batteries can have infinite utility if efficiently extracted, separated, and recycled.
“So, when the batteries are no longer suitable for vehicles, the first thing to do is to reuse them in some other application. Then, when the batteries have reached the end of their life, take them back and extract all that material,” she elaborates.
Global estimates, including those from the International Council on Clean Transportation (ICCT), suggest that approximately 50 percent of spent battery materials can potentially be mined, presenting an opportunity to significantly reduce the annual demand for these minerals by up to 28 percent over the next two decades (2050). In India, NITI Aayog forecasts that by 2030, there could be as much as 128 gigawatt-hours of recyclable batteries available, with EV batteries constituting 46 percent of this total.
India’s current recycling capacity stands at a modest two gigawatt-hours approximately and it would have to increase about 60 times in the next eight years.
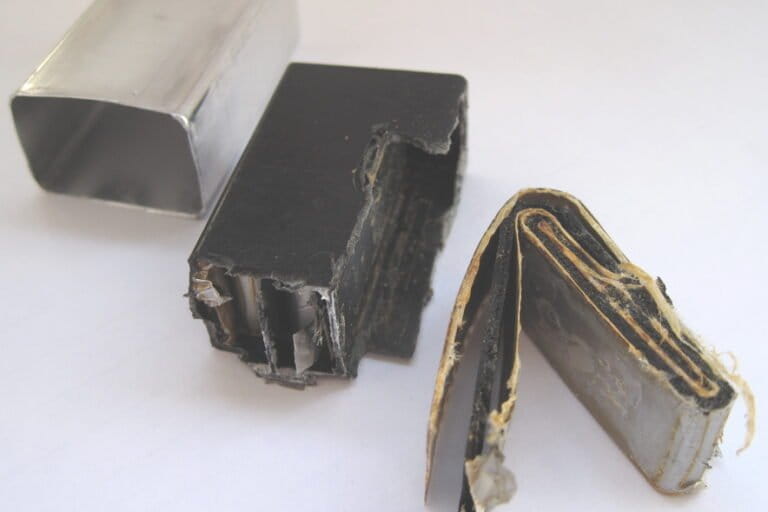
How can an EV battery be recycled?
A used lithium battery, if showing potential for a second life, is then refurbished to be used as a stationary storage unit. This potential is determined by the battery’s residual capacity, which has to be around 70-80% once it reaches the end of its previous life cycle as an EV battery.
As for batteries unsuitable for a second life, they are sent for recycling where they’re disintegrated into a black powder known as “black mass”, which is then further converted into a pink-coloured slurry. This slurry makes it easier to separate the ferrous and non-ferrous components and precious metals like cobalt, nickel, and lithium are then extracted through further refinement and ultra-refinement.
According to a CSE report published earlier this year, establishing a lithium-ion battery recycling facility with an annual capacity of 18,000 metric tonnes demands an investment ranging from Rs. 220 to 370 crores, whereas a lead-acid plant of similar capacity costs Rs. 4 crores. On a per-kilogram basis, recycling lead-acid batteries comes at a cost of Rs. 7, whereas lithium-ion battery recycling ranges between Rs. 100 and Rs. 150 per kilogram. Additionally, the operational expenses for a lithium-ion battery recycling unit are approximately 17 times higher than those for lead-acid battery recycling.
In 2022, NITI Aayog also proposed a new ecosystem with the battery as a service (BaaS) model which, among other things, also touches upon concerns about safety standards for batteries. Under battery swapping, EV users replace the discharged batteries with charged ones at the swap stations. A swapping station that is being installed at any particular location comprises multiple batteries getting charged constantly. An EV user can locate a swapping station, replace the depleting battery with a charged one, and put the empty battery on charge.
However, there are concerns about standards and the verification of battery quality and components.
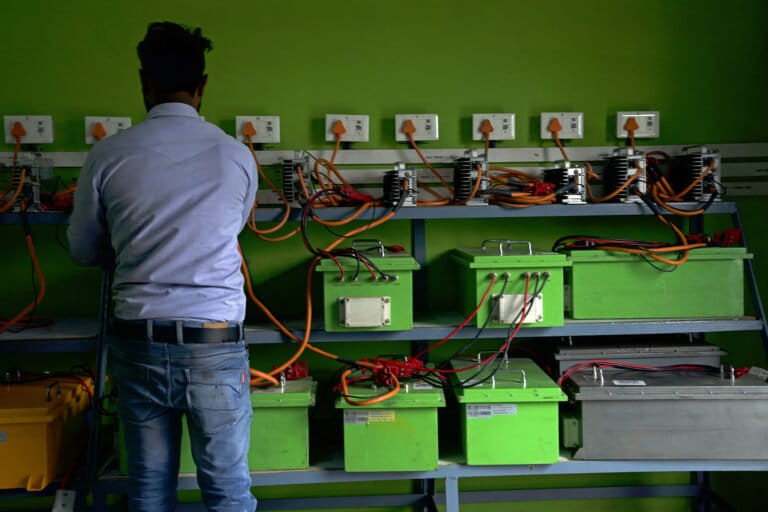
Battery swapping too, is a new concept. Mahesh says he believes that in a market that is price-sensitive, market forces and economic factors will play a significant role in the development of battery swapping. “We need to see how it (battery swapping) evolves, especially in the context of the informal sector, which has been involved in this segment for a long time. They might be better positioned to identify loopholes in the system and extract materials. However, this is something that should be closely monitored in the future.” she adds.
India has also published Battery Waste Management Rules from 2022, which is considered by energy experts as a positive step forward. These rules mandate that 90 percent of the materials we discard must be recycled and recovered by 2026, with 20 percent of that going into new batteries by 2030.
What makes recycling Li-ion batteries, a challenging task?
The current labelling requirements for EV batteries focus on heavy metals like mercury and cadmium, which are commonly found in traditional batteries. However, these labels do not mention the chemistries specific to lithium-ion batteries. This omission means that recyclers lack vital information about what they are dealing with, making planning and determining feedstock requirements for metal extraction, challenging.
Furthermore, it’s essential to know the battery’s chemistries for end-of-life and second-life purposes. Labels are just one aspect; there are many other pieces of information that could be helpful. For instance, details about the battery’s performance, health status, and history of use are critical. Documenting all this information benefits not only the recycling process but also various stakeholders. For example, it can help establish the residual value of the battery.
Roy Chowdhury points out another critical challenge, “One of the issues with EVs is the challenge of securing loan financing and obtaining insurance. Why is this problematic? It’s primarily due to the perceived lack of resale value. However, if we shift our perspective, we can see that these batteries actually contain valuable metals. The challenge lies in determining the extent of this value at the end of their life cycle. If we can accurately determine this value, many of these problems can be resolved. We could work backward to calculate it, and the impact would be profound across the entire life cycle of the EV and its battery. This valuable information could potentially be encapsulated in something like a battery identification number, akin to a passport – a battery passport number.”
How can India unlock the value and sustainability of EV batteries?
Countries worldwide are taking initiatives to strengthen the battery recycling industry and market. The European Commission has introduced new reforms that seek a carbon footprint declaration for batteries sold in Europe starting in 2024 through a digital tool called the ‘battery passport.’
Roy Chowdhury proposes the ‘battery passport’ concept in India too, as a unique ID for batteries that holds crucial details. These details include the battery’s chemistry, how well it has performed during its life, its current condition, its charging history, and any safety problems it has faced. With this data, recyclers can smartly decide what to do with the battery when it’s no longer useful and estimate its remaining value. This information can be valuable for producers in buyback deals and useful for bankers, insurers, and others who need to know the battery’s worth. However, it’s just one part of a larger puzzle and there are other factors to consider.
Another essential aspect Roy Chowdhury emphasises on, is efficient recycling, enabled by clear labelling and data digitisation systems. “Manufacturers must adhere to eco-design principles to simplify recycling processes. Additionally, adhering to testing, certification, and safety standards is crucial. Battery rules will need amendments to align with these changes.”
In sum, it’s clear that investing in the recycling industry is essential for India. However, the recycling industry that the country needs is highly capital-intensive and setting it up in a market with limited volume poses significant challenges. Determining viable business models and financing for such enterprises is crucial. Additionally, the recycling industry is not static; as battery chemistry evolves, recycling technology must keep pace. Also, there is no existing market to guide pricing and supply-demand dynamics. Therefore, India must address these significant gaps to proceed with EV battery recycling at a large scale, say energy experts.
Read more: India’s battery swapping policy to expedite EVs growth
CITATION:
Zheng, X., Liu, C., Deng, J., & Chen, X. (June 2018). A Mini-Review on Metal Recycling from Spent Lithium-Ion Batteries. Engineering, doi:10.1016/j.eng.2018.05.018
Niti Ayog and Green Growth Equity Fund Technical Cooperation Facility, 2022, Advanced Chemistry Cell Battery Reuse and Recycling Market in India, https://www.niti.gov.in/sites/default/files/2022-07/ACC-battery-reuse-and-recycling-market-inIndia_Niti-Aayog_UK.pdf
Breiter, A., Linder, M., Schuldt, T., Siccardo, G., & Vekić, N. (2023, March). Battery Recycling Takes the Driver’s Seat. McKinsey & Company. Retrieved from https://www.mckinsey.com/industries/automotive-and-assembly/our-insights/battery-recycling-takes-the-drivers-seat#/
Roychowdhury, A., & Mohant, M. (2023, August 02). Recycling EV Battery Material: Towards Material Security and Sustainability. Center for Science and Environment. https://www.cseindia.org/recycling-ev-battery-material-towards-material-security-and-sustainability-11803
Annual India EV Report Card: FY2023 https://jmkresearch.com/annual-india-ev-report-card-fy2023/#:~:text=While%20the%20annual%20EV%20sales,with%20~29%25%20market%20share
IEA. 2021. The Role of Critical Minerals in Clean Energy Transitions. Paris: IEA. https://www.iea.org/reports/therole-of-critical-minerals-in-clean-energy-transitions
IEA. 2023. Trends in electric light-duty vehicles. https://www.iea.org/reports/global-ev-outlook-2023/trends-in-electric-light-duty-vehicles
Tankou, A., Bieker, G., & Hall, D. (2023, February 16). Recycling Electric Vehicle Batteries. International Council on Clean Transportation. URL: https://theicct.org/publication/recycling-electric-vehicle-batteries-feb-23/
Banner image: Battery Pack for BMW-i3 Electric Vehicle. A used lithium battery, if showing potential for a second life, is refurbished to be used as a stationary storage unit. Photo by RudolfSimon/Wikimedia Commons.