- Spinning mills in Tamil Nadu started investing in renewable energy, primarily wind energy, more than 25 years ago to reduce electricity costs and greenhouse gas emissions.
- However, for this trend to continue and for newer mills to transition to clean energy, the textile industry must work through challenges in policy and energy banking, and find solutions for the intermittent wind power, aging turbines and the lack of land availability.
- While some mills in the state are beginning to invest in solar to complement wind energy, solar also faces challenges of high land cost and the high cost for the transmission infrastructure.
- Spinning mill owners call for clear wind and solar policies in the state and subsidies, to ensure a smooth transition to clean energy.
The textile industry in Tamil Nadu aims to transition entirely to renewable energy, as it costs lesser than the main grid energy, but the industry must work through challenges in policy and energy banking, and find solutions for aging turbines and the lack of land availability.
Textiles is one of the largest industrial polluters, contributing to about 10% of the global greenhouse gas (GHG) emissions due to its heavy reliance on electricity, primarily from fossil fuels. Globally, one trillion kWh (kilowatt hour) of electricity is consumed each year to produce 60 billion kilograms of fabric. Spinning mills that manufacture yarn/thread for weaving the fabric, constitute one of the most power-intensive stages in textile manufacturing. There are heavy machines involved at every step, starting from deseeding the cotton and arresting the cotton dust, to carding, combing and spinning into bales. Electricity is needed throughout the entire process.
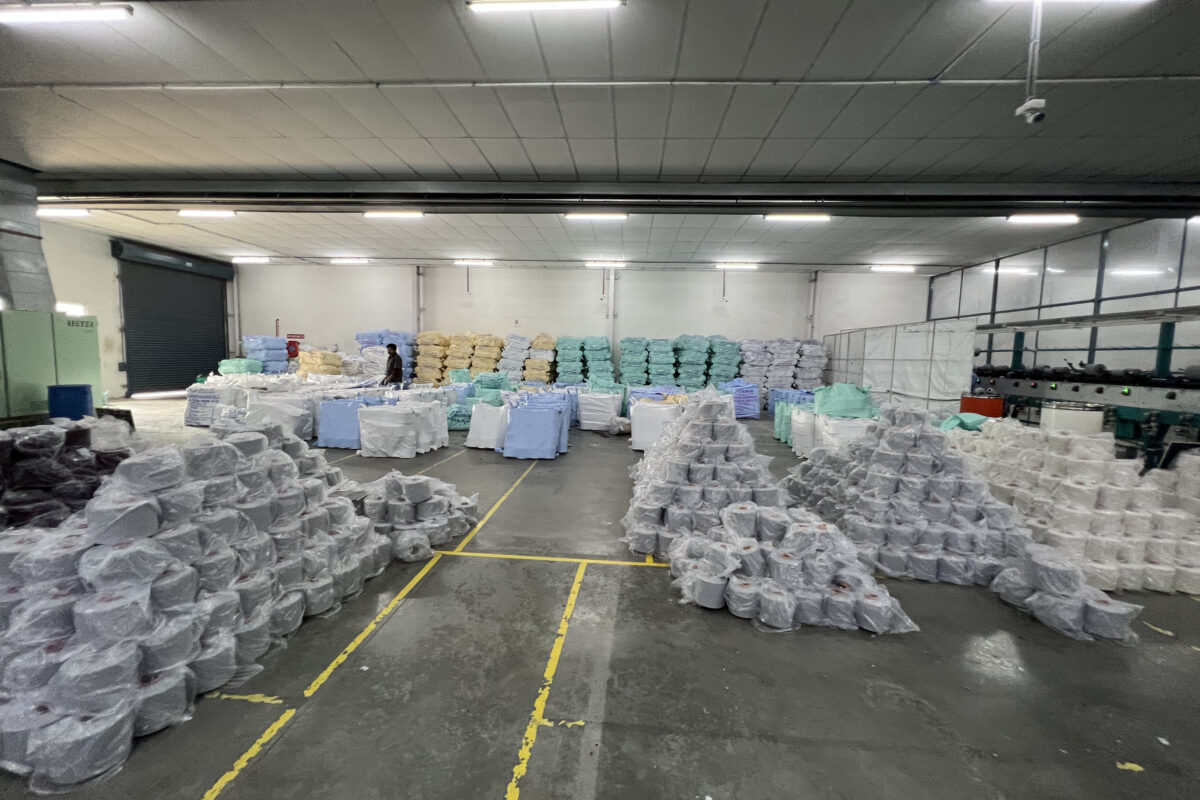
To combat the colossal GHG emissions, spinning mills in Tamil Nadu started their green journey more than 25 years ago. According to Tamil Nadu Spinning Mills Association (TASMA), its members have invested in wind energy across the windy passes of the state, such as Aralvaimozhi, Senkottah, Palghat and Andipatti. The capacities of the wind turbines vary from 225 kilowatts (KW) to 2.1 MW depending on the power requirement of the members’ mills for their own manufacturing demands.
Following the implementation of the Electricity Act in 1995 in India, the surge in electricity expenses prompted the textile industry to explore wind power technology as a cost-saving measure, explains S.K. Sundararaman, Chairman of the Southern India Mills Association (SIMA). “The Tamil Nadu textile industry pioneered the adoption of wind turbines in the 1990s for their manufacturing processes,” he tells Mongabay-India.
For instance, the L.S. Spinning Mills in the Theni district of Tamil Nadu began investing in wind energy 15 years ago. “Currently, we own nine windmills across Thoothukudi, Thenkasi, Tirunelveli, and Udumalpet, with a combined capacity of 6.05 MW,” says L.S. Prabhakaran, Managing Director of the mills, which consumes roughly 1,22,000 units of electricity each day.
Textile industries received a five percent interest subsidy previously under the Technology Upgradation Fund (TUF) for installing windmills, which led to the installation of 80% of the windmills in the state, amounting to about 1,500MW of wind power being once owned by textile industries, notes Sundararaman. “Currently, textile industries own 3,000MW wind power and 1,500MW solar power in the state, as the single largest captive consumer,” he adds.
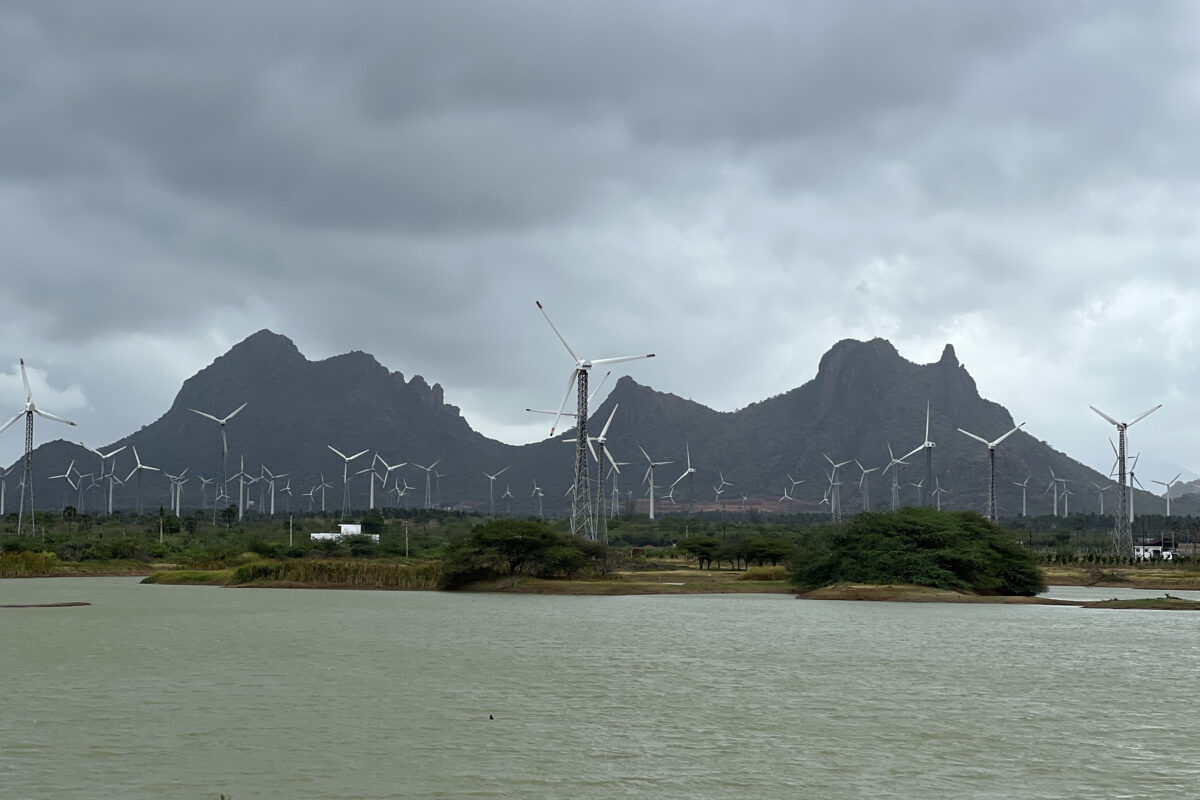
Challenges for windmills
While spinning mills are pioneers of a green transition in the state, they face several challenges with wind energy that stop them from powering their mills fully with renewable energy. The policy and financial structure for wind energy and the seasonality of wind power production are the main concerns for mill owners.
For example, ASM Spinning Mills located in Tiruppur, consumes 47,000 units of electricity per day to produce 21,000 kg of yarn daily. In 2019, the mills invested Rs. 13 crores to install a windmill in Kayathar, a town in Thoothukudi district , anticipating an annual generation of 50 lakh units. “However, the windmill generates only about 35 lakh units annually due to seasonal variations, resulting in an extension of the loan period from seven to eight and a half years,” Kiruthika Padmanabhan, CEO of the mills, tells Mongabay-India.
They were also unable to benefit from ‘wind energy banking’, due to the changing nature of Tamil Nadu’s energy banking policy. Energy banking is the exchange of electricity for electricity. It is an arrangement where surplus power generated in a particular period is fed into the grid. This surplus energy known as ‘banked energy’, is then supplied back during periods of low renewable energy generation.
“Investing in another windmill at such high costs wouldn’t be practical as it would produce excess energy that can’t be banked. Therefore, we’ve opted to concentrate on solar rooftops,” says Padmanabhan.
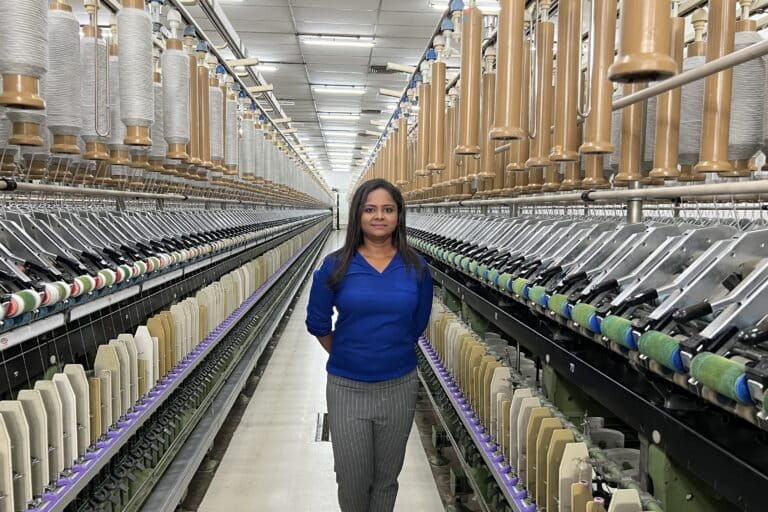
Although the Central Electricity Regulatory Commission (CERC) presently allows monthly energy banking for the power generators, instead of the previous policy of annual energy banking, it initially had no such provisions, notes Sundararaman.
“The government has already announced 50% reduction of solar networking charges for Micro, Small and Medium Enterprises (MSMEs). The peak hour charges for MSMEs have also been kept in abeyance till smart meters are installed. Reforms in the power banking system is under the active consideration of TANGEDCO,” clarifies V. Arun Roy IAS, Secretary to Government, Industries, Investment Promotion and Commerce Department.
However, Pradeep Natarajan, President of the Tamil Nadu Electricity Association, points out that industries are also subject to a 14% monthly fee for banking, in addition to charges for transmission, grid maintenance, distribution, and networking, without resulting in any loss for the government. “While wind energy generation is feasible for only half the year, how can a continuous process industry (such as the textile industry) sustain its use of renewable energy for the remaining portion of the year without banking?” he asks.
Natarajan underscores that improved energy banking facilities would create a level playing field, enabling the state textile industry to compete with counterparts in states like Gujarat and Maharashtra, where there exist power and industrial subsidies, as well as lower input and labour costs.
Meanwhile, sources from the state government suggest that the Tamil Nadu government may reinstate annual banking facilities for windmills soon. Reports indicate that the state industries minister TRB Rajaa, has been advocating for this initiative emphasising its significance for captive windmills.
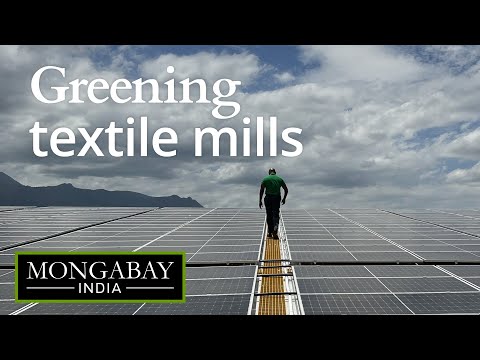
Repowering old wind mills
Wind turbines themselves pose some logistical concerns. One is the lack of space for expansion in the state. “The land availability in wind pass regions such as Thenkasi, Palakkad, and Kanniyakumari are exhausted with not much room for new windmills. However, the newer turbines in the market are said to be effective at harnessing wind energy at greater heights,” explains Prabhakaran. These newer, bigger turbines need good wind sites.
Another concern is the lifespan of windmills, which on average lasts 20-25 years. The Ministry of New and Renewable Energy (MNRE) has proposed a draft policy for repowering old wind turbines aiming to optimise wind-rich sites by upgrading to modern turbine technology, potentially increasing the capacity utilisation factor (CUF) from about 10-15% to 25-30%. According to a 2018 study, supported by MNRE, in India more than 10 GW of old wind turbines with less than 1 MW capacity are installed in wind-abundant sites. Repowering these sites with modern turbines will quadruple the energy generation.
Read more: Challenges in repowering Tamil Nadu’s aging windfarms
SIMA however, raises concerns that this could impact industry investments and questions the viability of the latest technology. “Industries cannot be forced to frequently update their technology, especially when the existing technology is green. Forcing constant energy reinvestment could impede our machinery upgrades,” says Sundararaman. He proposes establishing a fitness certificate for operating older turbines to ensure their continued efficiency, also highlighting that newer and larger wind turbines require several more acres of land.
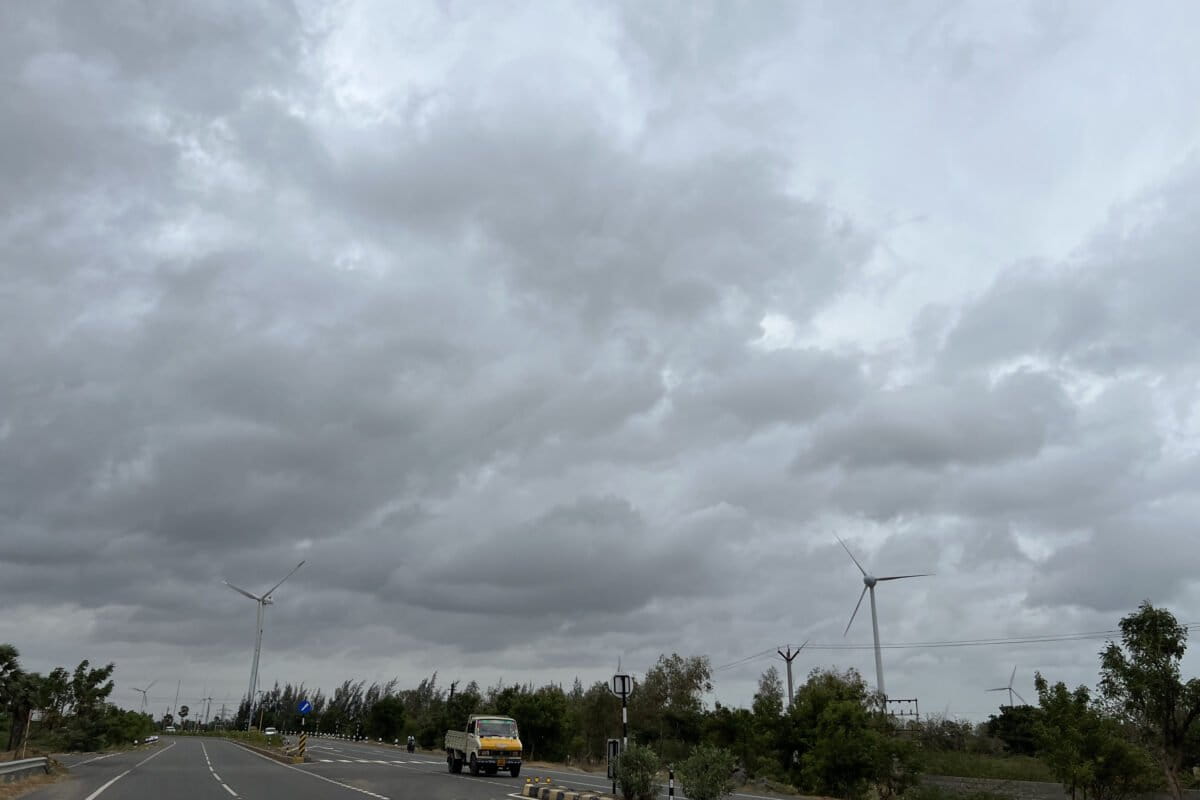
Yet, Francis Jayasurya, Director-India, Global Wind Energy Council argues that repowering old wind turbines is essential, and that new technology could operate with higher efficiency even in low wind conditions. He stresses the need for a comprehensive government policy and financial incentives to drive the adoption of new technology, including benefits like captive power taxation advantages, as repowering initiatives may not yield the desired results without such backing.
Others meanwhile believe in the potential of the offshore windmills proposed in the Gulf of Mannar region, to solve the textile industry’s energy problem. “If the central government subsidises the high cost of undersea cabling, the project’s feasibility would improve. The exact amount of central government incentives will be known next year, offering hope for the revival of wind installations in Tamil Nadu,” shares Kasthuri Rangaiyan, Chairman, Indian Wind Power Association (IWPA).
Read more: Offshore wind in Gulf of Mannar
Weaving solar into the picture
Some companies like Raghul Spinning Mills in Rajapalayam, have abstained from investing in wind power. “The wind power produced exceeds the grid’s capacity during peak seasons. So, windmills are intermittently stopped which doesn’t sound wise from an investment point of view,” says P. Devaraj, Managing Partner at Raghul Spinning Mills.
Others have been slowly shifting towards solar energy. BIRIN Spinning Mills, which consumes 35,000 units per day, has recently installed ground-mounted solar as its first RE initiative. “Excluding wind power is impossible when we move towards 100% RE sources, especially considering the solar power generation is limited to daylight hours. But solar is becoming an important part of the energy basket,” shares Muthu Venkatesh, Technical Director of the Mill in Tiruppur.
Venkatesh chose to invest in automation due to rising labour costs. “However, we entered into a group captive consumer agreement with another producer, securing green power at Rs. 6.50 per unit compared to the average grid cost of Rs. 8 per unit. This resulted in savings of approximately Rs. 60,000 per day and Rs. 25-30 crores annually on electricity bills,” he says.
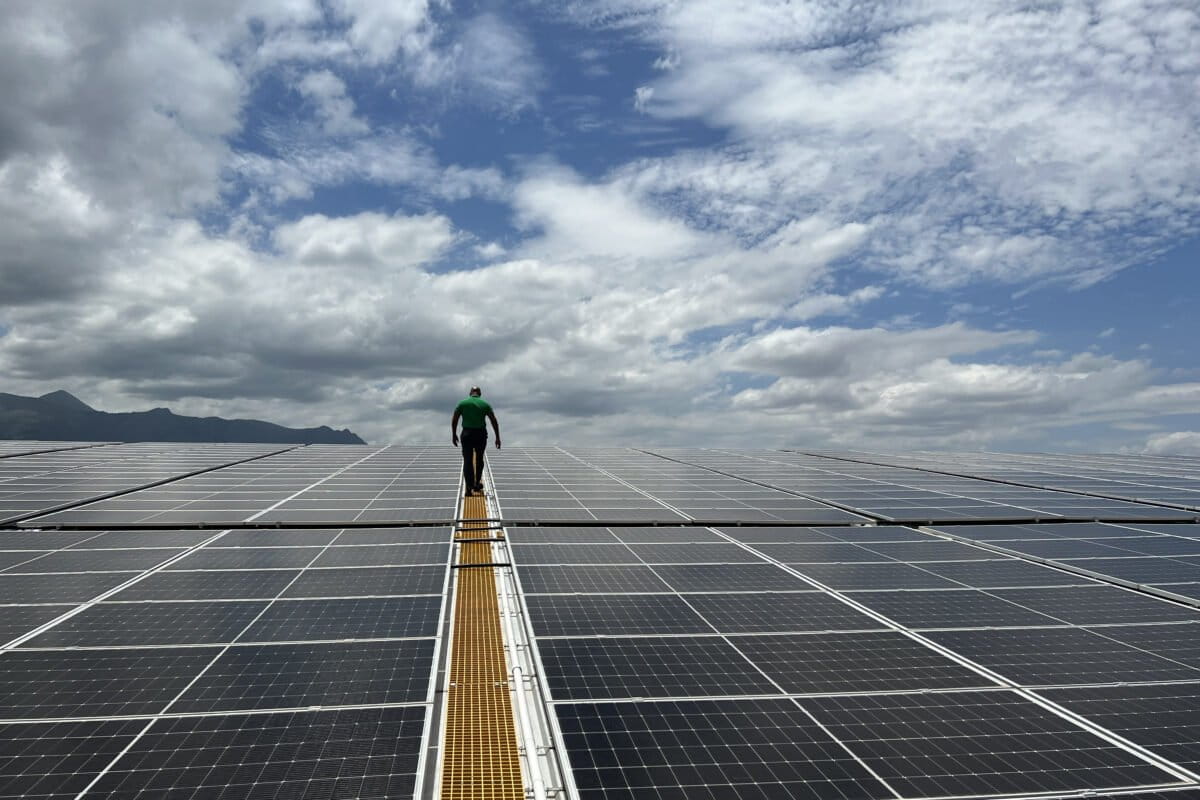
“It is permitted to only use 20% of the solar energy generated during TANGEDCO’s 30% daily peak hours TANGEDCO’s designated peak hours (6am-10am and 6 pm-10pm). So, it becomes mandatory to buy power from the grid or the Indian Energy Exchange (IEX),” says Venkatesh.
However, he is still compelled to switch to solar energy as leading manufacturers in the industry have widely adopted renewable energy, significantly reducing their electricity costs to approximately Rs. 15 per kg of yarn, while his cost remains at Rs. 25 per kg, even after purchasing green power at a reduced rate.
Venkatesh considered solar rooftops but found that there is a longer payback period of seven years due to wheeling charges (fee paid to transport electricity), as opposed to six years for ground-mounted solar. “Presently, the cost per megawatt for ground-mounted solar is approximately Rs. 4.5 crore. However, when the panels and the setup are procured in bulk, suppliers offer a reduced rate for the equipment of Rs. 10-15 lakh per megawatt. To leverage the benefit, four friends of mine collaborated to initiate a 15 MW solar project spanning 45 acres, which saved me approximately Rs. 60-70 lakh for my 6 MW share,” says Venkatesh.
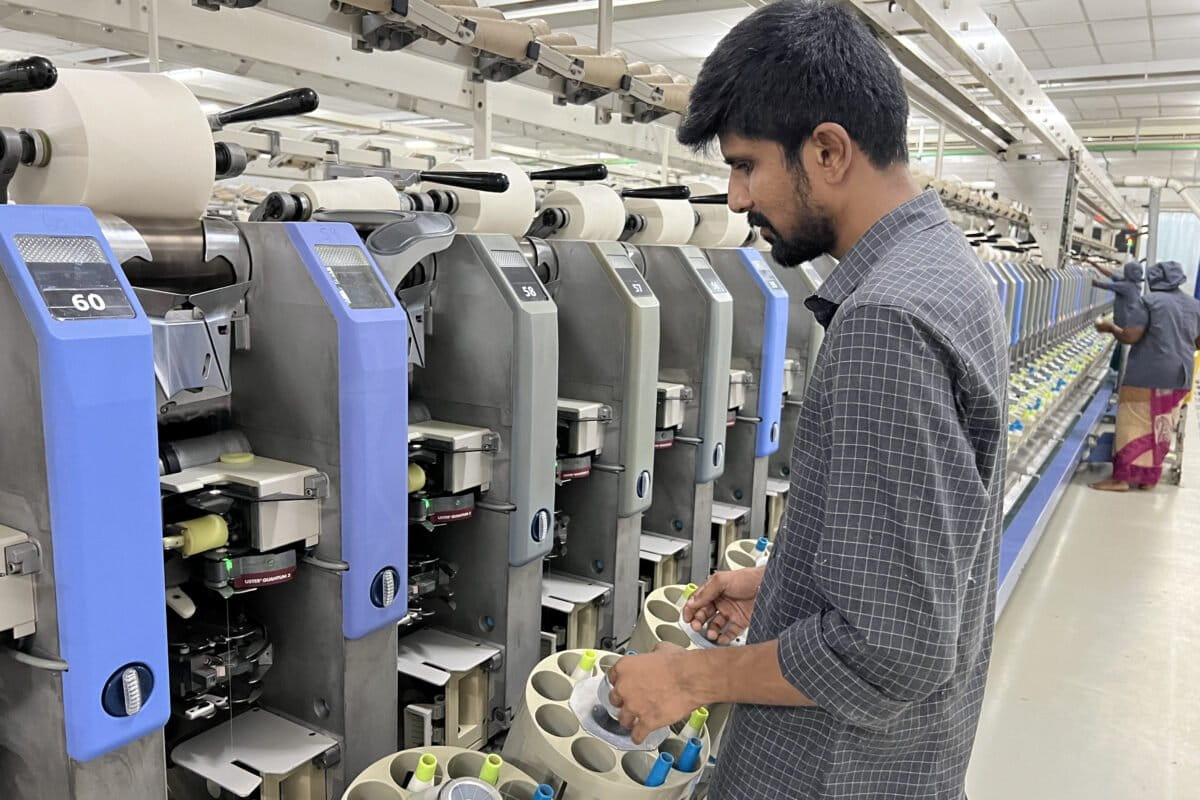
Challenges with solar energy
Solar energy however, does come with its own obstacles. Solar panels cannot be installed anywhere; they must be strategically located, considering cheaper land parcels and the grid’s availability to accommodate the generated energy. It is also important to keep in mind the kind of soil in the land chosen — black soil, for example, can become ‘clayey’ during the rainy season impeding maintenance work, explains Devaraj.
“In addition, we must secure various approvals and navigate through formalities since we are installing lines in public areas,” says Venkatesh, whose solar project is supposed to fulfil 60% of his company’s power requirement.
Finding a suitable substation is another significant challenge. Land prices tend to rise once a substation is registered for a solar project, compelling the need to purchase land a few kilometers away from the substation, which then incurs higher costs for power lines and transformers.
“Industries have to pay 96 paise per unit in network charges for merely connecting their solar rooftop systems to the grid to establish a reference current, even though there is no power drawing or exporting,” explains Sundararaman. It is especially hard for small-scale mills that rely on these setups.
“Factoring in variables like cloudy days, their payback period could exceed a decade. Eliminating this charge, which only generates Rs. 3.70 crore for the government, would save many small textile industries,” Pradeep Natarajan shares. And the costs keep adding up. “Over the last two months, we’ve relied 100% on renewable energy due to reduced production in the industry downturn. We still had to pay the government Rs. 26 lakh per month as charges alone,” worries Padmanabhan.
“On average, the wheeling and transmission charges cost us around Rs. 6,000 per MW per day, and we further lose 8-10% of our generation during transmission,” claims Devaraj.
Although no subsidies exist for RE projects currently, like the previously allowed TUF, the government provides collateral-free loans for solar rooftops with panels manufactured in India, Padmanabhan notes, emphasising the efficiency variations depending on where the panels are made and how they are installed. She sees great potential in innovations for solar electricity storage using batteries.
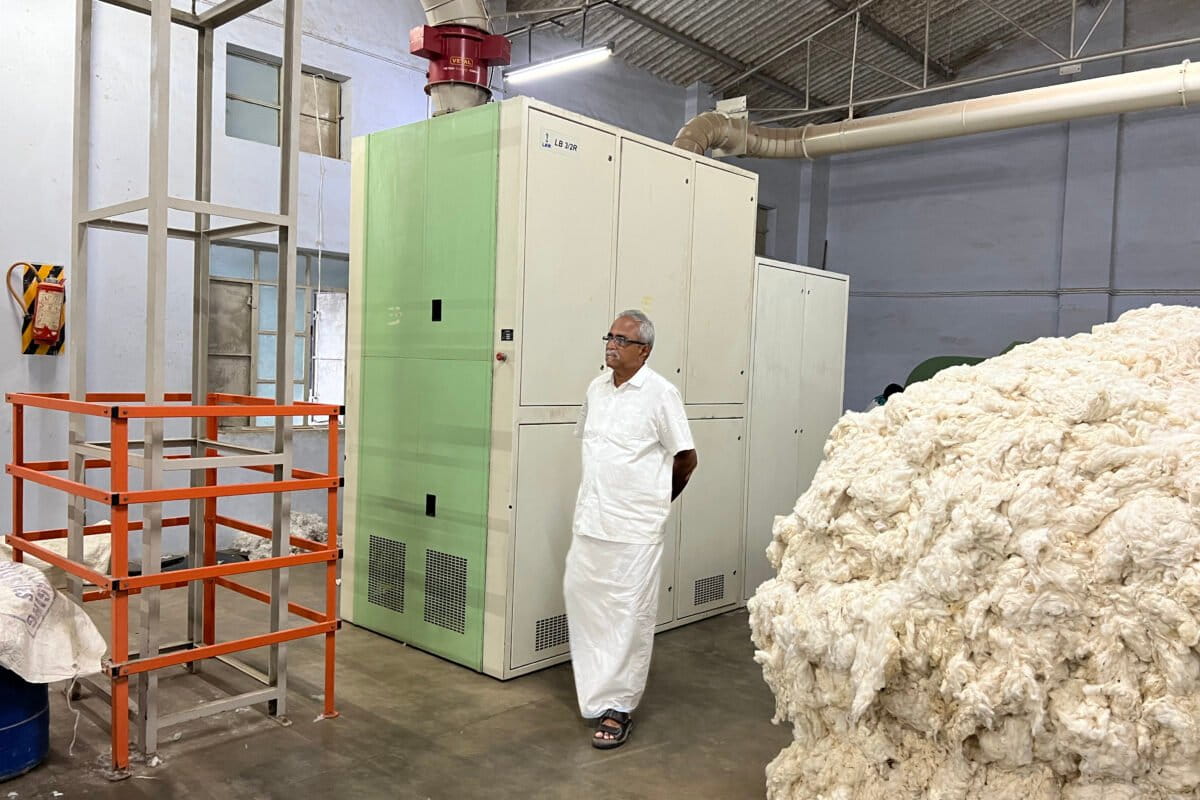
Achieving 100% renewable energy in the textile industry
Mill owners express mixed opinions on shifting to 100% renewable energy. Some opine that it is not profitable. “We do not plan to transition entirely to renewable energy. When the demand for power is lower during market fluctuations or power shutdowns, the produced energy can’t be stored and it would lapse,” clarifies Devaraj. “How would we manage power on cloudy days or low wind season, considering textiles is a continuous process industry?”
Others like Padmanabhan aspire to transition to 100% renewable energy, to align with their goal of becoming a fully sustainable brand. “However, the challenge lies in balancing the intermittent nature of solar and wind energy, which cannot meet our needs around the clock,” she adds. “In our factory, during peak seasons, windmills generate 35,000 units per day and solar rooftop produces 10,500 units per day roughly. Our monthly electricity bill used to be around Rs. 95 lakhs, but with solar and wind power compensating 50% of our energy needs, we’ve cut it down to about Rs. 65 lakh a month.”
L.S. Spinning Mills in Theni claims that it achieves 100% of its electricity generation from renewable sources. It boasts 6.05 MW of wind power, 10.5 MW of ground-mounted solar, and 3.2 MW of rooftop solar. Prabhakaran shares, “Despite higher prices when compared to today, we embraced solar technology (about 15 years ago), understanding its cost-effectiveness in the long-term. Recently, we also installed a solar rooftop on our factory’s 1,50,000 sq. ft. roof, approximately equivalent to four acres.”
The Executive Director at LS Spinning mills, Harshavardhanaa, explains that combining both wind and solar power could be efficient long-term. “A 10MW solar plant yields around 2MW of usable power, and a 10MW wind turbine produces 3MW of actual power, with respective efficiencies of 20% and 30%. Therefore, deploying a hybrid a model where solar panels and wind turbines coexist in the same location offers an efficient and sustainable way to maximise renewable energy utilisation in a single space,” he says.
Policy gap
The National Institute for Wind Energy (NIWE) has estimated that the Tamil Nadu has over 68.75 GW of onshore wind power potential and 35 GW of offshore wind potential. Similarly, the state’s solar energy potential is estimated to be 17.67 GW. So far, only one-tenth of the state’s wind potential and one-third of its solar potential have been harnessed.
”At a time when the Tamil Nadu Electricity Board (TNEB) is grappling with meeting its power demand, it encourages the Ministry of Micro, Small and Medium Enterprises (MSME) to invest in wind power by offering a 2% charge for banking and wheeling, leading to a substantial increase in wind energy investments in Tamil Nadu,” shares Rangaiyan.
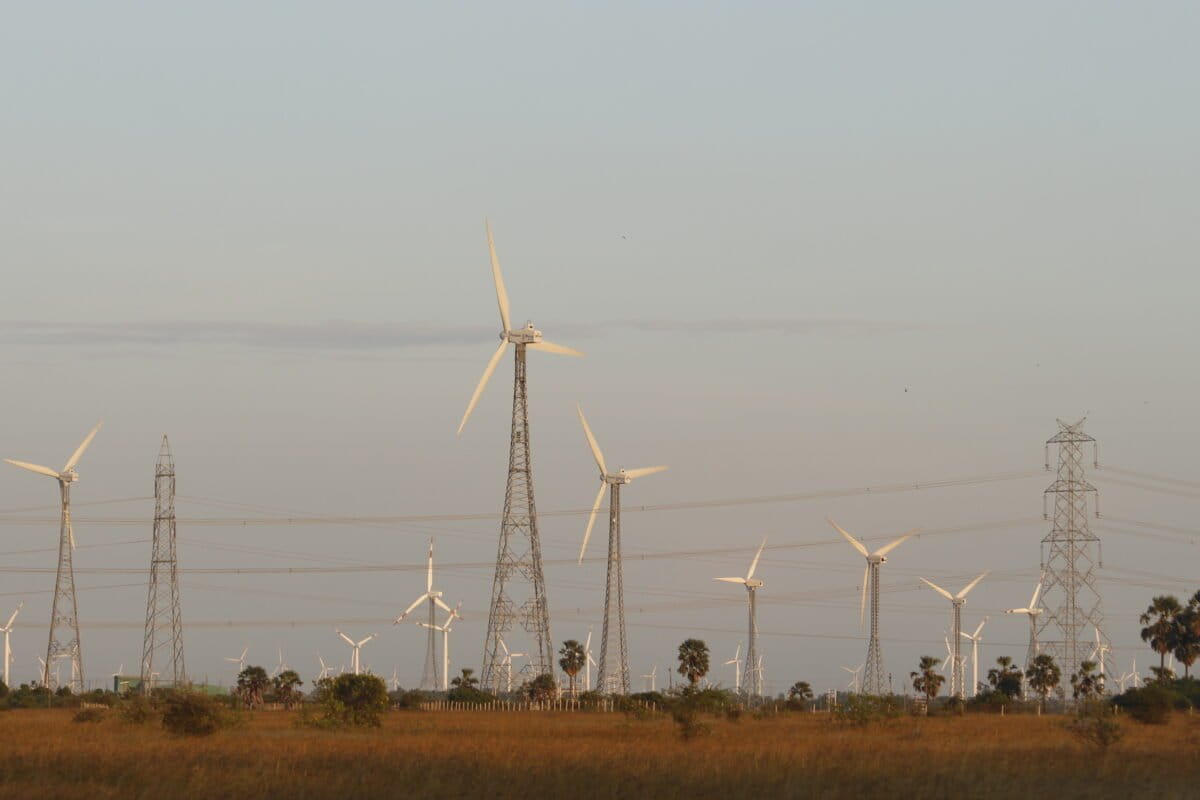
“Despite regular payment of operation and maintenance charges by investors in wind and solar energy in Tamil Nadu, the energy transmission infrastructure is in a state of disrepair. Substations, feeders, and lines are inadequately maintained, lacking spare parts for timely replacements. Failure of equipment in the transmission system affects heavy evacuation leading to inadequate utilisation of wind energy, as the grid support for evacuation is unavailable,” says K. Venkatachalam, Chief Advisor, TASMA.
He adds that the state of Tamil Nadu has no wind energy policy, and though it once had a solar energy policy in 2012, which was renewed in 2019, both have expired now. “The absence of clear policy measures is discouraging our members from investing in the renewable energy sector,” he says.
Editor’s note: This story was updated on November 26, 2023, to include a response about energy banking from sources in the Tamil Nadu state government.
This story was produced with support from Internews’ Earth Journalism Network.
Banner image: Raghul Spinning Mills in Tamil Nadu. Spinning mills that manufacture yarn/thread for weaving the fabric, constitute one of the most power-intensive stages in textile manufacturing. Photo by Gowthami Subramaniam/Mongabay.