- Aligarh hosts approximately 6,000 lock-making facilities, collectively contributing to 75% of locks manufactured in India.
- The lock industry in Aligarh relies on the strategic use of scraps generated at the pre-manufacturing level, post-manufacturing remnants, and materials sourced from dismantled vehicles, to repurpose metal waste into locks.
- Recycling car scraps to manufacture locks, a trend observed over the past 10-15 years, reduces the demand for new resources and minimises energy consumption and also decreases the carbon footprint associated with steel production.
On a typical Monday morning, 47-year-old Sajid Ali, a third-generation artisan from Aligarh, meticulously feeds steel sheets into a roller, which flattens them further getting them ready for the subsequent stages of lock manufacturing. Despite their fresh appearance, these sheets bear subtle signs of prior use and occasional unevenness – a testament to their recycled origins. Sajid, a resident of the Shah Jamal area in Aligarh, Uttar Pradesh, explains, “These are not fresh sheets. Extreme precision and uniformity are not always required in the hardware industry, allowing us to utilise these less uniform sheets. That is why we use car scraps.”
Having started working as a locksmith at age 21, Sajid now produces around 35 to 40 locks per day of varying sizes, which require approximately 15 kg of car scraps. Procuring these materials is no small feat. At the crack of dawn, artisans like Sajid and their assistants converge at Saroj Nagar and a few other areas, where negotiations with scrap dealers unfold amidst a bustling backdrop. After rounds of bargains over prices, these artisans secure the raw materials essential for the locks they aim to craft.
These locks, crafted from old sheets, gleam with the promise of safeguarding valuable assets. They are sought after not only across different parts of the country but also abroad, underscoring the city’s status as a prominent hub for lock manufacturing. With more than 6,000 lock-making facilities registered, Aligarh boasts a rich history dating back to the Mughal era, but it was the British who are credited with streamlining it as a major economic activity.
Situated about 150 km southeast of New Delhi, Aligarh witnesses around two lakh artisans who are busy creating handmade locks. From large-scale factories to humble household kitchens, the city’s lock-making industry thrives, contributing to around 75% of all locks produced in India. Apart from registered businesses, an estimated 3,000 homes also actively participate in this industry, evident from lock-making tools and components scattered throughout local residences.
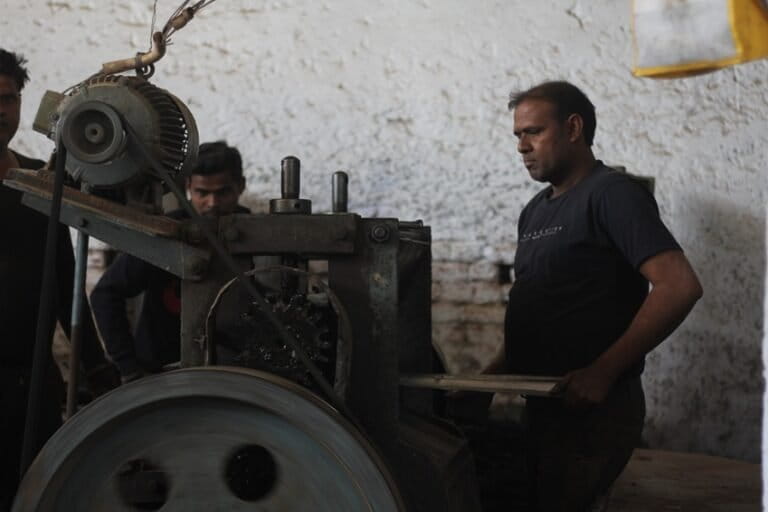
Repurposing metal waste
Lock manufacturing relies heavily on high-quality raw materials such as stainless steel, iron, brass, and nickel. However, in the recent years, there has been a notable shift within the industry towards utilising car scraps as a primary resource, according to local manufacturers.
Sajid Ali recalls a time when scrap dealers, locally known as kabaadiwala, would arrive with carts overflowing with various brass scraps, including mugs, pans, and gas knobs. Recognising the potential in these discarded materials, manufacturers began exploring alternative sources for raw materials, leading to a transformative revelation that waste could be repurposed.
This newfound perspective sparked a wave of innovation within the industry. With the automotive sector generating substantial amounts of metal waste, artisans and factory owners saw an opportunity to tap into this resource. The idea of using car scraps for crafting intricate locks proved to be innovative and cost-effective, addressing the scarcity of raw materials faced by manufacturers.
Sagar Gupta, Managing Director of G.Bhaiyaji Secure Homes, sheds light on the industry’s eco-conscious approach. “We procure scrap material from large furnaces provided by car manufacturers, often obtaining surplus materials of varying thickness through online bidding. Despite being labelled as scrap by manufacturers, we find these materials to be of premium quality for our purposes,” he explains. The industry’s preference for malleable square sheets, ideal for lock and hardware manufacturing, drives the innovative repurposing of materials.
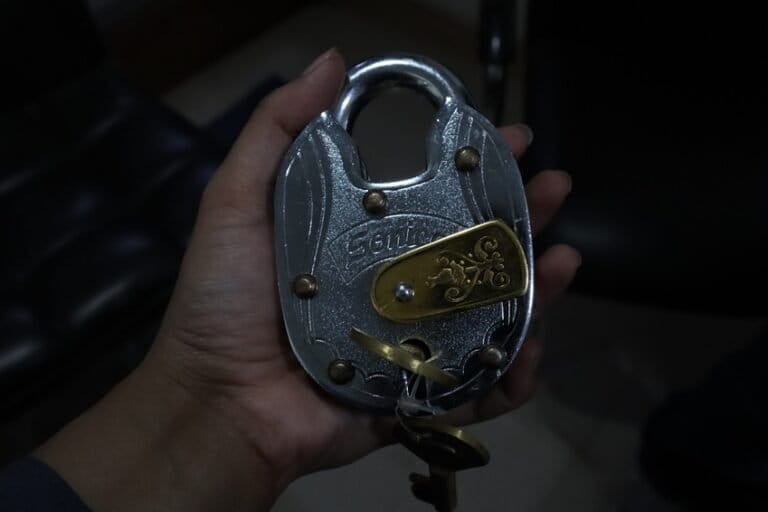
Ratna Vadra, a faculty member at the Institute of Management Technology, Ghaziabad, has written a paper on the Aligarh lock industry highlighting its challenges. She says that concepts such as ‘learning by doing’ have a significant bearing on the Aligarh lock industry, especially in material sourcing. Through hands-on experience, lock manufacturers gain knowledge and skills in sustainable material sourcing. For instance, they test different recycled materials, judge their suitability, and discover which suppliers offer the most economical and ecologically responsible solutions, she says.
The economics of recycling
Ali reflects on the surge of interest in using car scrap some 15 years ago. “Although the industry has always relied on various types of scraps, not exclusively car scraps but also household scraps of brass, aluminium, iron, and steel in a limited capacity. The sheet coils that used to come to us had a width ranging from about 600 mm to over 1800 mm, neither of which met our requirements nor were cost-effective for us.”
Many small-scale factory owners informed Mongabay-India that the shift towards car scrap was driven by cost-effectiveness. Compared to new sheets, which are more expensive, car scraps offer a cheaper alternative. Additionally, the nature of these scraps makes them suitable for producing small parts, further enhancing their utility. By carefully managing how these scraps are used—determining the number of pieces that can be produced and their combinations—they claim to have achieved efficient and effective production processes.
The cost of stainless-steel sheet coils, such as the Jindal SS 304, varies with thickness and dimensions. For instance, a 3-4 mm thick sheet costs around Rs. 250 per kg in India, and the price generally increases with thickness. Gupta told Mongabay-India that the scrap material they acquire through bidding typically costs them between Rs. 100 and Rs. 150 per kg.
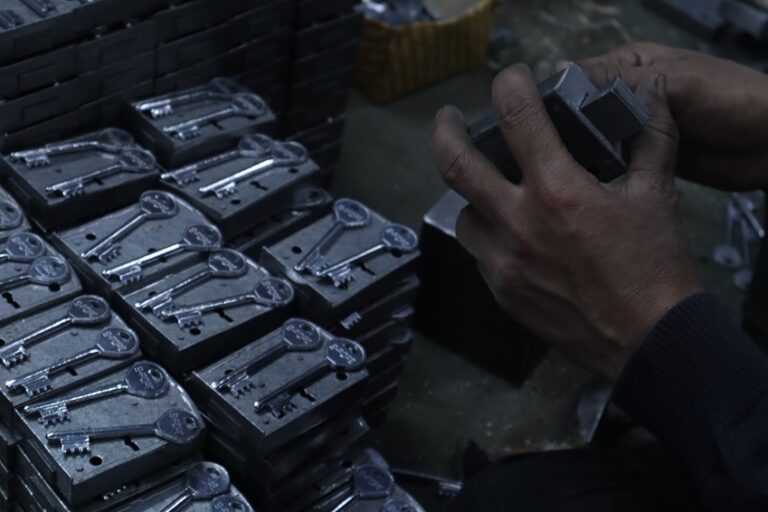
The quest for sustainability also drives exploring diverse scrap sources beyond traditional practices. “In the lock industry, we look everywhere for scrap materials that can be reused, even from unexpected places like leftover sheets from computer manufacturing. After these sheets are cut down for their original purpose, we take the remaining pieces and turn them into parts for locks. This approach not only saves materials but also helps the environment by reducing waste,” says Pradeep Maheshwari, Proprietor, Brassco Enterprises.
The commitment to recycling extends further, as evidenced by the strategic use of cylinder knobs. For example, the government collects certain items like cylinder knobs, sells them at auction, and then the factory owners buy them to use in their locks. “Even the waste from our casting process, ‘lochan,’ is recycled again and remoulded into brass form at a fraction of the cost of new materials,” Maheshwari further explains.
Discussing the cost-effectiveness of recycling brass, Maheshwari emphasises that with the price of brass at Rs. 300 per kg, the recycling cost for this waste material is approximately Rs. 75. This cost includes the expenses associated with melting the waste and giving it a proper shape.
Hari Om, president of the Aligarh Locks Manufacturers and Traders Association, sees the increased use of scraps due to the competition with Chinese products. He says, “We don’t receive the government support needed; we have to pay market price for iron or steel sheets. For instance, while raw brass material might cost Rs. 300 per kg in China, it costs us Rs. 500 per kg, which has led to a shift towards using scraps in our industry.”
Stiff competition from Chinese products is a big challenge for Aligarh lock manufacturers, experts believe. Ratna Vadra highlighted these challenges in her 2020 paper. In addition to competition from Chinese manufacturers, she listed several other factors, such as dwindling demand for handmade locks and the adverse effects of government policies such as demonetisation and GST implementation on the Aligarh lock industry. Vadra says that the affordable pricing Chinese competitors offer may require more work for Aligarh producers to match, even with creative strategies like using recycled materials.
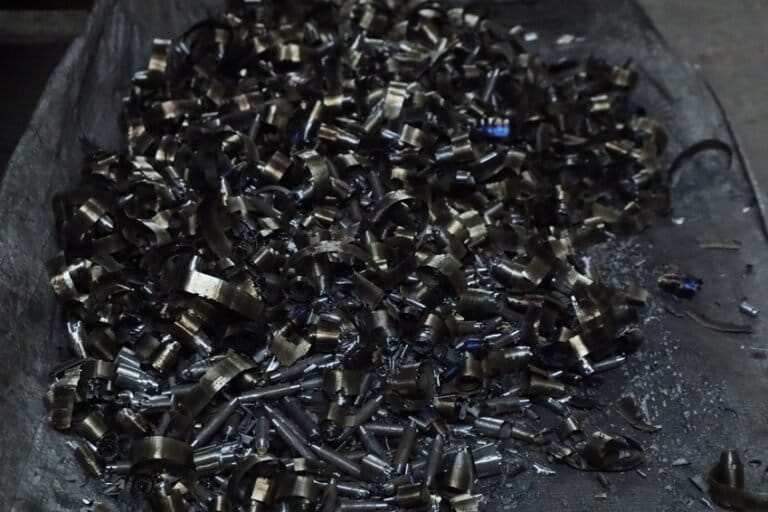
Reducing the carbon footprint
Furthermore, Gupta from G.Bhaiyaji Secure Homes emphasises the environmental benefits of utilising these scraps. He states, “By incorporating these materials into our production process, we reduce the demand for new resources and minimise energy consumption. This sustainable approach conserves energy expended in material creation and transforms waste into valuable products.”
The iron and steel industry, essential for lock manufacturing, carries a substantial environmental burden due to its energy-intensive processes. Traditional steelmaking emits significant carbon dioxide, approximately 1.7 to 2.2 metric tonnes per tonne of steel produced. India generates around 25 million tonnes of scrap metal annually and imports an additional five million tonnes. To address steel requirements and emissions, the government aims to increase the share of scrap in steel production to 50% by 2047.
Furthermore, data on car manufacturing waste in India underscores the urgency of adopting sustainable practices. A joint study by the Central Pollution Control Board (CPCB) and GIZ estimated that there were about 8.7 million end-of-life vehicles (ELVs) in India in 2015, with projections suggesting a 250% increase to approximately 21.9 million by 2025. The increase in scraps emphasises the need for innovative recycling initiatives like those in Aligarh.
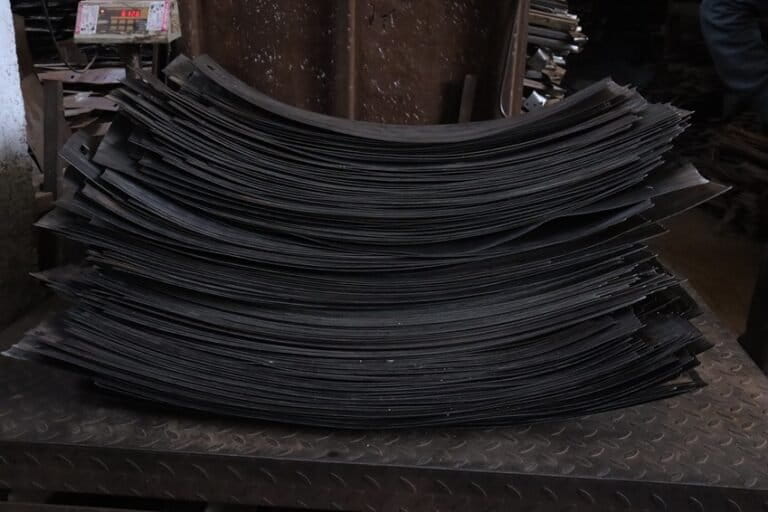
Anumita Roy Chowdhury, Executive Director, Centre for Science and Environment (CSE), explains that Aligarh’s lock manufacturers are reducing the demand for newly produced steel by repurposing car scraps and other recycled materials. This practice not only limits waste generation but also decreases the carbon footprint associated with steel production. For instance, reusing one tonne of steel scrap in manufacturing can save approximately 1.5 tonnes of carbon emissions compared to producing a new tonne of steel. Given Aligarh’s significant output, the city’s recycling innovation could substantially reduce the industry’s overall carbon footprint, though precise figures would require detailed analysis.
However, Chowdhury points out that these practices are often informal and lack a structured framework. To fully leverage these efforts, a more systematic approach to waste management across the industry sector is needed. By better mapping where and how waste is generated and offering robust support to small and medium-scale enterprises, we can significantly enhance their economic benefits while advancing sustainability goals.
Read more: Stitching sustainability amidst climate change challenges
Banner image: A scrap godown in Aligarh. Locksmiths in Aligarh use car scraps as a raw material. Photo by Zoya Ada Hussain/Mongabay.